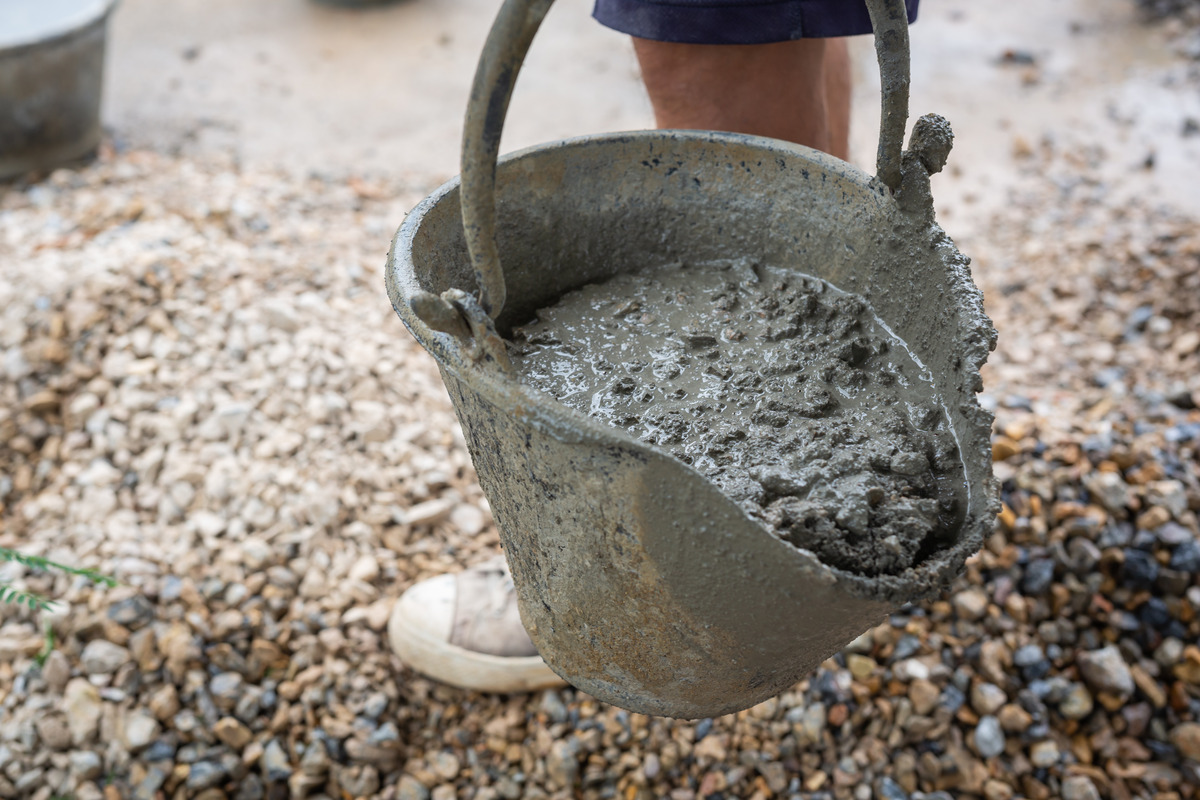
When it comes to construction, the debate on the right concrete mixing method — ready mix concrete vs. on-site mixing has always held a central spot. Both methods have gained attention and use in construction projects worldwide but the question remains, which one is superior? The answer, as often, lies in understanding the pros and cons that each option brings to the table.
In this article, we will extensively explore the advantages and shortcomings of both ready mix concrete and on-site mixing to help you choose the most cost-efficient and quality-effective method for your construction project. Our in-depth examination will hinge on factors such as cost, quality, convenience, and environmental impact — vital elements that make or break the success of your project. So whether you are a professional in the construction sector or a novice looking to navigate this concrete jungle, stay tuned, and let’s delve into the world of concrete mixing.
Ready Mix Concrete
Ready mix concrete is a specialized type of concrete that is manufactured in a factory or batching plant, according to a predefined engineered mix design. It is subsequently delivered by a truck mixer to the construction site in a ready-to-use state.
Pros of Ready Mix Concrete
Convenience and Time-Saving
Being pre-mixed in controlled environments, ready mix concrete significantly reduces the time and labor needed for batching, mixing and ensuring the right proportions of raw materials on-site. This efficiency can be a game-changer, especially in large-scale projects with tight deadlines or where swift completion is necessary. The fact that the mixture arrives on-site ready to use means less hassle for the construction team, allowing them to focus on other critical elements of the project.
Consistent Quality
The mixture is prepared in industrial settings armed with automated equipment and under strict quality control, so it guarantees a consistent, high-quality product every time, ensuring the strength and durability of the structures built with it. It comes with a precise mix, tailored to specific needs and applications, reducing the risk of human error during mixing. This consistent quality ultimately translates to enhanced structural integrity, improved durability, and less maintenance for a building.
Reduced Labor and Equipment
The significant reduction in labor and equipment requirements on-site leads to cost savings and streamlined processes. Since the concrete mixing is performed off-site at the batching plant, the need for a continuous manual labor force and heavy-duty mixing equipment on the construction site, along with their associated costs, is greatly minimized. This, thus decreases the risk of accidents at the job site associated with concrete production. Also, less labor on site means less required management and supervision, resulting in reduced indirect costs and logistical complications.
Cons of Ready Mix Concrete
Cost
Ready mix concrete is produced in a controlled factory environment and delivered to the construction site in ready-to-use form, so it often incurs higher costs due to transportation and the quality control measures that need to be put in place. And while it’s cost-effective for larger projects due to its efficiency and reduced need for on-site labor and equipment, it may not be as beneficial for smaller projects where the amount of concrete required may not justify the costs involved. Besides, any unpredicted changes or delays in construction can lead to concrete wastage, adding to overall costs.
Limited Adjustability
When you opt for ready mix concrete, changes in the mixture once it’s been prepared at the plant and is en route or already at the job site are extremely limited, if not impossible. This means if there is a sudden change in your project—be it an alteration in design or dealing with unexpected weather conditions—you may not have the flexibility to adjust the consistency or quantity of the mix as might be necessary. This makes this type of concrete less adaptable to changes that commonly occur in construction projects.
Transportation Issues
Given its nature, ready mix concrete needs to be used within two hours of batching at the plant to maintain its properties — which places a strict timeline on the delivery and use of the concrete, thereby creating logistical challenges. Any delay in transit due to factors such as traffic or long distances can result in the concrete setting before reaching the construction site, rendering it unusable. This not only leads to material waste but also unplanned additional costs and potential project delays.
On-Site Mixing
On-site mixing, as the name suggests, involves the production of concrete right at the construction site. This method provides builders with the flexibility to adjust quantities and the mixture composition based on the evolving needs of the project. It comprises batching the raw materials—cement, aggregate, and water— in specific proportions directly on the site, as and when required. This process generally includes the use of a mobile mixer or a stationary mixer
Pros of On-Site Mixing
Cost Savings
With on-site mixing, the cost of transporting ready mix concrete from the plant to the construction site is eliminated. The use of an on-site mixer also allows for precise control over the volume of concrete produced, reducing wastage and saving costs on excess materials. There’s also less risk of having to deal with or pay for unused concrete because you’re only mixing what you need when you need it.
Customization
On-site mixing is a method that allows for real-time adjustments to the concrete mix to suit the specific requirements of different parts of a construction project. As the constituents are mixed on-site, the proportions and type of mix can be altered for different loads as per the evolving needs of the construction project. Whether the project calls for a stronger mix for a particular section or a more workable mix to facilitate pouring, on-site mixing can cater to these demands on the fly.
This flexibility for customization, however, requires experienced workers who can adjust the ratios precisely to maintain the strength and performance qualities of the concrete, emphasizing the importance of skilled labor in this process.
Transportation Issues
Unlike ready mix concrete, which must be transported from the production plant to the construction site, on-site mixing completely eliminates this logistical challenge. The raw materials are brought to the site and mixed as and when required, alleviating the pressure of ensuring the concrete’s delivery in a usable state within a strict timeline. This method thus offers a solution to projects located in remote areas or hard-to-reach sites where the transportation of ready-mixed ones might be challenging or costly.
Cons of On-Site Mixing
Labor and Time Intensive
On the flip side, on-site mixing can be significantly labor and time-intensive, which is one of its primary drawbacks. Getting the precise mix of concrete requires skilled labor and close attention to detail, and this process needs to be repeated for each batch of concrete made. This not only increases the project costs due to the requirement of skilled laborers but also extends the timeline of the project because producing each
batch of concrete on-site is more time-consuming than having it delivered ready to use.
Quality Control Challenges
Quality control poses a significant challenge when opting for on-site mixing. As the concrete is mixed on the spot by manual labor or using a standard mixer, maintaining the consistency and quality of the mix can be difficult, especially across multiple batches. Factors such as the accuracy of measurement, the specific composition of the mix, or even the conditions on the site, including weather, can affect the final product’s quality. This variation in the quality of the concrete could lead to discrepancies in the structural integrity of different parts of a project, potentially compromising the strength and longevity of the construction.
Waste and Overordering
Despite the perceived control over concrete quantity in on-site mixing, it can often lead to waste through over-ordering of raw materials. This is particularly prevalent where there’s uncertainty about the exact quantity of concrete required for a job, or where contingencies for changes or errors are being considered. Over-ordering means that excess materials need to be stored, managed, and eventually disposed of if unused, resulting in wastage.
On the other hand, underestimating the concrete required might lead to supply shortages, delaying the project or causing hiccups in the construction flow. Also, concrete that is mixed but not used immediately can lead to spoilage.
Key Takeaway
Both ready mix concrete and on-site mixing methods have their unique pros and cons, making each better suited for specific types of construction projects. And the choice between the two essentially boils down to an evaluation of the project’s requirements, the available resources, and the anticipated challenges. By understanding the benefits and drawbacks of each method, you can make an informed decision that best suits your construction needs, ensuring successful completion while maintaining quality and cost-effectiveness. It’s the careful balance of these factors that will determine the success of not just the choice of concrete, but the overall construction project.